Are you involved in logistics and aiming to align your operations with GDP standards? Navigating the complexities of Good Distribution Practice in pharma (GDP Pharma) is crucial to ensure quality compliance in the supply chain. In this article, we will explore 6 proactive strategies to minimize the risk of customer claims by employing a problem-solution-proof approach, with pharma supply chain software.
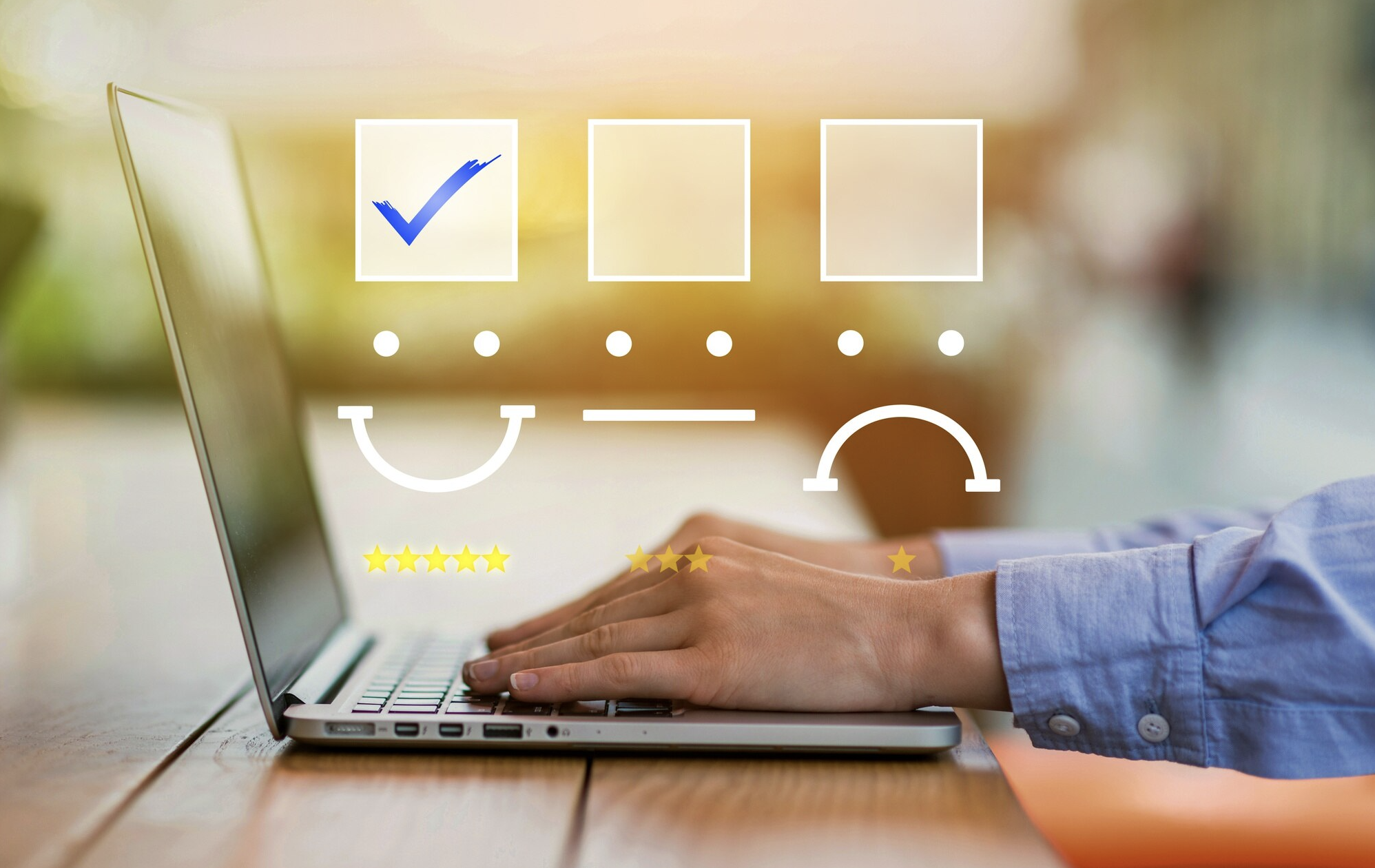
Identify and mitigate Risks for GDP in the pharmaceutical industry
In GDP logistics - or GDP Pharma - , non-conformances can lead to customer dissatisfaction and claims. These deviations from standard practices can compromise product quality and undermine customer trust. It is essential to maintain strict adherence to GDP logistics guidelines to protect your company's reputation and minimise the risk of customer claims.
For example:
Non-Conformances in temperature-controlled shipments
A failure to maintain the required temperature range during transit can lead to compromised product quality. For instance, GDP in the pharmaceutical industry, where companies transport sensitive vaccines. If the temperature is not meticulously monitored and controlled throughout the journey, because of outdated data for example, it can result in the degradation of the vaccine's efficacy, leading to severe financial implications and regulatory repercussions. In such instances, the batch must be recalled and destroyed—a process requiring coordination between the sender’s and receiver’s QA teams.
Often, the receiver is awaiting approval to sell and has pending orders, leading to delivery shortfalls. There must be proof of the products' instability and subsequent destruction, ensuring quality and safety standards are upheld.
Inadequate Record-Keeping in Storage Facilities
Another substantial risk involves inadequate record-keeping practices, particularly in storage facilities. Imagine a scenario where a warehouse fails to maintain accurate records of incoming and outgoing goods, expiration dates, and batch numbers. This lack of meticulous documentation can result in difficulties during inspections, as the inability to trace products can lead to compliance violations and subsequent fines, not to mention that even basic operations like picking and finding the correct items to compile an order are already challenging.
GDP in pharmaceutical industry: be prepared for customer inspections and quality audits
Proactive preparations of internal audits within your logistics can significantly reduce the likelihood of customer claims in the GDP pharmaceutical industry. Implementing quality risk management principles assists in pinpointing and rectifying potential issues before they escalate into customer grievances. An electronic Quality Management System (QMS) is instrumental in ensuring process efficiency and adherence to quality standards.
The importance of an eQMS for GDP in Pharmaceutical industry
A robust Quality Management System (QMS) is the cornerstone of quality assurance and customer satisfaction. The GDP software that we call a logistics quality management solution serves as the backbone of quality assurance in logistics, providing a centralised platform for documentation, process control, and risk management. It serves as a centralised tool for:
-
Documenting processes, which aids in demonstrating compliance and operational integrity during customer inspections. This includes records of shipments, temperature controls, and compliance certificates.
-
Standardising processes to consistently meet GDP pharma standards, reducing the risk of quality failures that lead to customer claims.
-
Employing real-time monitoring to swiftly identify and correct deviations, and preventing issues that could result in customer dissatisfaction for GDP in pharmaceutical industry.
Inspections & Audits: what are the results for GDP in pharmaceutical industry if there is failure?
Non-compliance within the logistics sector can significantly disrupt the supply chain. Such disruptions can lead to unwelcome delays in the delivery of products and administrative fines, which can range from thousands to millions of dollars, depending on the seriousness of the infraction. Additionally, non-compliance can undermine trust and cooperation among suppliers and distributors, which are essential for efficient logistics operations and have huge impact on the company’s brand name and reputation in the market. It also affects customer satisfaction, raising concerns regarding the quality and safety of the products being delivered.
To avoid these consequences, it is essential for logistics companies to engage in a series of strategic actions. They must carry out regular internal audits, which are crucial for ensuring that operations consistently align with Good Distribution Practice (GDP) standards. Continuous staff training programs are another key element, as they keep the workforce informed of the latest best practices and regulatory updates.
Furthermore, the implementation of a robust pharma supply chain software is imperative. Such a system oversees compliance, and addresses any issues that might arise before they can escalate into larger problems.
CAPA Management: a preventative strategy for GDP in pharmaceutical industry
Corrective and Preventive Actions (CAPA) management is a strategic component in mitigating the risk of customer claims in GDP pharma logistics. A proactive approach involves identifying potential issues, implementing corrective actions, and instituting preventative steps to ensure ongoing compliance and customer satisfaction.
Proactive CAPA Management
Strategic CAPA management in logistics operations enables companies to:
-
Undertake comprehensive root cause analysis to pinpoint the origins of issues that could lead to customer claims.
-
Apply corrective actions to resolve immediate problems and preventive actions to avoid their occurrence.
-
Implement preventive strategies to anticipate and mitigate potential issues, maintaining a reliable and customer-focused GDP logistics system. Discover how Bizzmine's QMS helps you stay compliant gdp compliant in the pharmaceutical industry.
Implementing Good Documentation Practices in pharmaceutical industry
- Centralised control of all compliance-related documents facilitates easy access and management.
- Electronic Signature add a layer of security and authenticity, which can be critical in resolving customer claims.
- Automated workflows for approval in a QMS platform ensure documents are reviewed and approved efficiently, leaving a clear audit trail.
- Version control and Change Management ensure that only the current, approved documents are in use, preventing misunderstandings that could lead to customer claims.
- Real-time monitoring and reporting capabilities provide oversight of the documentation process, allowing for quick action if issues arise.
- Training records within the QMS ensure that all personnel involved in handling documentation are competent and understand GDP requirements in the pharmaceutical industry, thus reducing errors that could result in customer claims. Ask one of our consultants about our eQMS for GDP compliance.
Principles of Quality Risk Management for GDP in pharmaceutical industry to enhance customer satisfaction
Incorporating quality risk management principles is fundamental in reducing the occurrence of customer claims. A digital QMS can integrate risk assessment tools into daily operations, offering features like real-time risk monitoring, mitigation workflows, and comprehensive reporting and analysis. GDP in the pharmaceutical industry should be taken seriously together as a valid GDP certification is essential to work as a logistics company in the pharma transportion business.
Navigating through the complex landscape of logistics and Good Distribution Practice (GDP pharma compliance) can be challenging, but it is essential for minimising customer claims and maintaining customer satisfaction. The six strategies outlined provide a framework not just for avoiding customer claims, but also for strengthening the resilience of your supply chain. From proactive risk identification to the implementation of quality risk management principles, each step is vital for achieving operational excellence and delivering products that meet both regulatory and customer standards
With our guidance, you can improve customer satisfaction and boost your supply chain's resilience. Simply book a timeslot with one of our GDP consultants to discover more.
You may also like: