CAPA implementation: 6 common mistakes made in CAPA Quality Management
Within the CAPA (Corrective and Preventive Actions) quality management process, there are several common mistakes that organizations can make. These mistakes can undermine the effectiveness of CAPA implementation and interfere with the improvement of quality systems. Here are some of the most common mistakes reported to us when discussing CAPA Management and CAPA implementation.
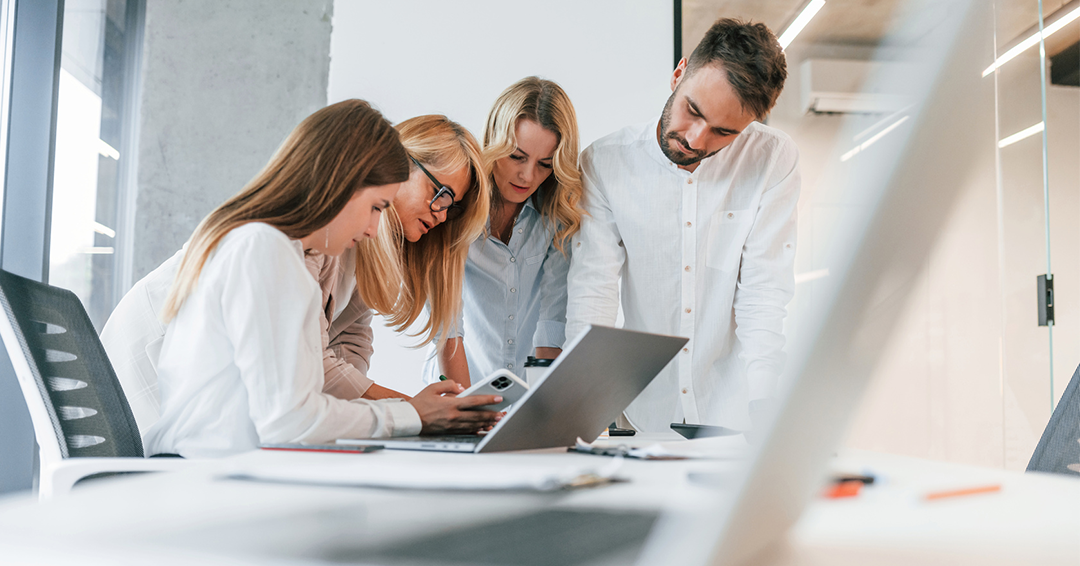
IN THIS ARTICLE
1. Insufficient Root Cause Analysis 2. Lack of decent documentation 3. Failure to implement Preventive Actions 4. Lack of cross-functional collaboration and inadequate stakeholder involvement |
1. CAPA implementation mistake: insufficient Root Cause Analysis
One of the most critical aspects of CAPA management is identifying the root cause of a problem. However, organisations often rush or overlook this step, resulting in ineffective corrective actions. It's important to conduct a thorough and systematic root cause analysis to properly address the underlying issues.
2. CAPA implementation mistake: lack of decent documentation
Proper documentation management is crucial in CAPA management to maintain a clear record of issues, investigations, actions taken, and outcomes. Unfortunately, many organisations fail to maintain accurate and detailed documentation, which can be a barrier to traceability and understanding the CAPA process. Ensure that all steps, findings, and actions are properly documented for future reference and audits.
3. CAPA implementation mistake: failure to implement Preventive Actions
CAPA management is not only about corrective actions, but also about implementing preventive measures to avoid the recurrence of problems. Neglecting this aspect and focusing only on immediate remedial actions can lead to recurring problems. It is important to identify and implement preventive actions to eliminate the root causes and avoid similar issues in the future.
4. CAPA implementation mistake: lack of cross-functional collaboration and inadequate stakeholder involvement
Effective CAPA management requires collaboration between different departments within an organisation, not just the involvement of the quality team. Failure to engage the right stakeholders or involve them at the right stages of the CAPA process can lead to incomplete information, ineffective solutions, and a lack of ownership. It is important to involve relevant people with the necessary knowledge and expertise by implementing the right software for Training management.
5.CAPA implementation mistake: inadequate training and awareness
CAPA management requires a well-trained and informed workforce, keeping track of the right training records. Organisations often neglect to provide sufficient training to employees involved in the CAPA process, leading to inconsistencies, misunderstandings, and ineffective actions. Ensure that employees are trained in the CAPA process, including root cause analysis techniques, documentation practices, and the importance of preventive actions.
6. CAPA implementation mistake: no monitoring and reviewing
The effectiveness of CAPA management should be monitored and reviewed regularly to ensure that the actions taken are achieving the desired results. Unfortunately, organisations often overlook this critical step and fail to track the progress of CAPA implementation or conduct follow-up audits. Regular monitoring, evaluation, and feedback are essential to measure the success of the CAPA process and make necessary adjustments.
To optimise CAPA Quality Management, organisations should seek to avoid these common mistakes by fostering a culture of continuous improvement, emphasising thorough analysis, promoting accountability, providing appropriate training, and implementing robust documentation and monitoring.
Bizzmine can help you to avoid these 6 common mistakes. Book some time with one of our consultants, and learn more on how to make CAPA implementation more efficient.